คอมพิวเตอร์, ระบบนำทาง GPS, โทรศัพท์มือถือ, กล้องดิจิทัล, อินเทอร์เน็ต และอีกหลากหลายเทคโนโลยีที่เราใช้ในชีวิตประจำวันวันนี้ แท้จริงแล้วมีอายุมากกว่าที่เราคิด แนวคิดของเทคโนโลยีเหล่านี้เริ่มขึ้นตั้งแต่ช่วงทศวรรษ 1960 และ 1970 เป็นยุคแห่งการสร้างนวัตกรรม
นวัตกรรมหนึ่งในนั้นก็คือเทคโนโลยีดิจิทัลทวิน (Digital Twin) ที่นักวิทยาศาสตร์และวิศวกรในปัจจุบันมองว่าเป็นหัวใจสำคัญของการปฏิวัติอุตสาหกรรมครั้งใหม่ โดย Digital Twin คือการสร้างคู่แฝดดิจิทัลของวัตถุทางกายภาพ ซึ่งการมีคู่แฝดดิจิทัลนี้ทำให้เราสามารถติดตาม ตรวจสอบ วินิจฉัยการทำงานของอุปกรณ์และระบบต่างๆ อีกทั้งสามารถคาดการณ์การบำรุงรักษาได้แบบเรียลไทม์ เป็นการเพิ่มประสิทธิภาพการดำเนินงานอย่างมีนัยสำคัญ
แบบจำลองทางกายภาพของยานอวกาศ NASA คือ จุดเริ่มต้นของ Digital Twin
แนวคิดเริ่มต้นของ Digital Twin มีรากฐานมาจากภารกิจในอวกาศขององค์การบริหารการบินและอวกาศแห่งชาติหรือ ‘นาซ่า’ (NASA) เมื่อประมาณ 60 ปีที่แล้ว เนื่องด้วยการปฏิบัติภารกิจในอวกาศมีค่าใช้จ่ายและความเสี่ยงสูงมาก ดังนั้นการจำลองสถานการณ์บนพื้นโลกเพื่อเตรียมความพร้อมก่อนเผชิญสถานการณ์จริงในอวกาศจึงเป็นภารกิจที่สำคัญ
แนวคิดที่เรียบง่ายนี้ยังคงเป็นประโยชน์หลักของ Digital Twin ในปัจจุบัน โดยคำว่า “Digital Twin” ได้เป็นที่แพร่หลายและรู้จักมากขึ้นใน ค.ศ. 2010 โดย Michael Grieves และ John Vickers จาก NASA และเป็นจุดเปลี่ยนจากเทคโนโลยีที่ใช้เฉพาะในการสำรวจอวกาศสู่การปฏิวัติอุตสาหกรรม

การเติบโตของ Digital Twin และ IoT
หาก Digital Twin เป็นหัวใจสำคัญของการปฏิวัติอุตสาหกรรมครั้งใหม่ ข้อมูล (Data) ก็เปรียบเสมือนเส้นเลือดที่ไปหล่อเลี้ยง Digital Twin ยิ่งมีข้อมูลมากการจำลองก็ถูกต้องและแม่นยำยิ่งขึ้น การเพิ่มขึ้นอย่างก้าวกระโดดของการใช้อุปกรณ์ IoT (Internet of Things) ทั่วทุกมุมโลก ยิ่งเสริมสร้างการเติบโตของการใช้ Digital Twin จากข้อมูลของ Statista พบว่ามีอุปกรณ์ IoT ที่ใช้อยู่ในการงานทั่วโลกถึง 18 พันล้านเครื่องในปี 2024 และคาดว่าจะเพิ่มขึ้นมากกว่าสองเท่าภายในปี 2033 โดยอุปกรณ์ IoT เหล่านี้จำนวนมากถูกนำไปใช้ในโรงงานทั้งภาคอุตสาหกรรมและภาคการผลิต ซึ่งช่วยให้วิศวกรสามารถจำลองกระบวนการการทำงานทุกแง่มุมในสภาพแวดล้อมดิจิทัลเสมือนจริง ตั้งแต่ตัวผลิตภัณฑ์ เครื่องจักรไปจนถึงสายการผลิตทั้งหมด
ซีเมนส์กับการขับเคลื่อนการพัฒนา IoT และ Digital Twin
ซีเมนส์ได้ให้ความสำคัญกับเทคโนโลยีการประมวลผลข้อมูลตั้งแต่ทศวรรษ 1970s และได้มีบทบาทสำคัญในภารกิจสำรวจอวกาศผ่านซอฟต์แวร์และโซลูชันดิจิทัล ซึ่งต่อมาได้ถูกนำมาประยุกต์ใช้และสร้างการเปลี่ยนแปลงอย่างมากในภาคการผลิต การพัฒนาทางเทคโนโลยี เช่น ระบบอัตโนมัติและระบบควบคุม และระบบดิจิทัล (Digitalization) ในยุคเริ่มแรกได้กลายเป็นรากฐานสำหรับเทคโนโลยีที่ขับเคลื่อน IoT ในปัจจุบัน
ด้านเทคโนโลยี Digital Twin นั้นเริ่มแรกถูกออกแบบมาเพื่อจำลองและติดตามระบบที่มีความซับซ้อนในกิจการอวกาศ โดยการสร้างคู่แฝดดิจิทัลของวัตถุทางกายภาพทำให้วิศวกรสามารถคาดการณ์ได้ว่าส่วนประกอบของยานอวกาศจะตอบสนองต่อสภาพสุดขั้วในอวกาศอย่างไร ปัจจุบัน ซีเมนส์ได้นำ Digital Twin มาใช้ในภาคการผลิต ด้วยความสามารถในการทดสอบและปรับปรุงระบบอย่างมีความแม่นยำสูงในโลกเสมือนก่อนปฏิบัติจริงทำให้ผู้ประกอบการสามารถเพิ่มประสิทธิภาพของสายการผลิต คาดการณ์ความต้องการการบำรุงรักษาของเครื่องจักรและอุปกรณ์ ลดเวลาในการหยุดทำงาน (downtime) และลดของเสีย โดยไม่ต้องเสี่ยงกับการทดลองที่มีค่าใช้จ่ายสูงในโลกจริง
ในปี 2012 ซีเมนส์ได้ร่วมมือกับ NASA ในภารกิจสำรวจดาวอังคาร “Curiosity” โดยบริษัทฯ ได้จัดหาโซลูชันซอฟต์แวร์ที่ใช้ในการพัฒนา จำลอง และทดสอบยานสำรวจดาวอังคาร ต่อมาในปี 2015 ซีเมนส์ได้นำเสนอแนวคิด Digital Twin สำหรับใช้งานภาคอุตสาหกรรมที่งาน Hannover Messe ประเทศเยอรมนี พร้อมนำเสนอเทคโนโลยีสำหรับอุตสาหกรรมในสาขาต่างๆ รวมถึงอุตสาหกรรมการผลิตแบบต่อเนื่องและการสร้างเครื่องจักร
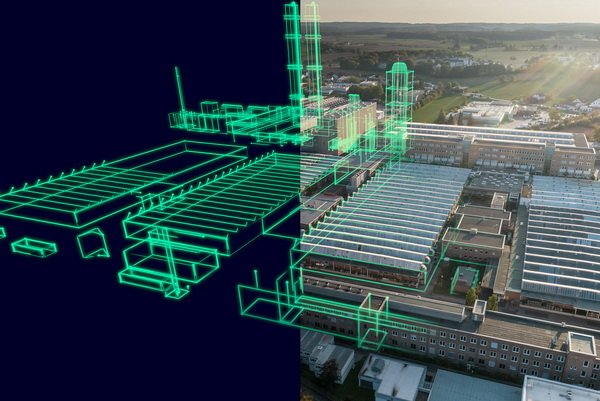
รากฐานของอุตสาหกรรม 4.0 และอนาคตของโรงงานอัจฉริยะที่ยั่งยืน
ปัจจุบัน Digital Twin เป็นหัวใจของการเปลี่ยนผ่านกระบวนการอุตสาหกรรมไปสู่ยุคดิจิทัลหรืออุตสาหกรรม 4.0 Digital Twin ไม่เพียงมีประโยชน์ในขั้นตอนกระบวนการดำเนินงาน แต่มีประโยชน์อย่างมากนับตั้งแต่เกิดไอเดียหรือโมเดลธุรกิจขึ้น
วันนี้การสร้างโรงงานอัจฉริยะจะเกิดในรูปแบบ Digital Twin ก่อนแล้วจึงค่อยก่อสร้างเป็นโรงงานจริงภายหลัง โดยการจำลองที่แม่นยำนี้ไม่เพียงช่วยเลี่ยงอุปสรรคที่อาจเกิดและเสริมสร้างความปลอดภัย แต่ยังช่วยในการออกแบบกระบวนการทั้งหมดให้ทำงานได้อย่างมีประสิทธิภาพสูงสุด เพื่อสร้างโรงงานแห่งอนาคตที่ให้ผลผลิตสูงและมีความยั่งยืน
นี่เป็นเพียงจุดเริ่มต้น ต่อไปการผสมผสานเทคโนโลยี Digital Twin กับ AI จะช่วยให้คอมพิวเตอร์สามารถออกแบบผลิตภัณฑ์และกระบวนการที่เหมาะสมได้อย่างอิสระ ซึ่งจะสนับสนุนผู้ประกอบการในอุตสาหกรรมในการตัดสินใจเกี่ยวกับนวัตกรรม วางแผน ดำเนินงาน และการบำรุงรักษาต่างๆ
การผสานโลกจริงและโลกดิจิทัลเข้าด้วยกัน
Digital Twin เป็นตัวอย่างของการเชื่อมต่อโลกจริงกับโลกดิจิทัลเพื่อสร้างผลลัพธ์ที่ยั่งยืน ด้วยการสร้างคู่แฝดดิจิทัลของวัตถุทางกายภาพ ธุรกิจจะได้ข้อมูลเชิงลึกที่ช่วยเพิ่มประสิทธิภาพการดำเนินงาน คาดการณ์ความท้าทายที่อาจเกิดขึ้น และสร้างนวัตกรรมอย่างมีความรับผิดชอบ
สิ่งสำคัญที่เราต้องตระหนักคือ โลกของความเป็นจริงและผู้คนยังคงเป็นศูนย์กลางของการตัดสินใจในการใช้เทคโนโลยีอยู่เสมอ เทคโนโลยีขั้นสูงอย่าง AI หรือเทคโนโลยีอื่นๆ ไม่ใช่จุดมุ่งหมายสุดท้ายในตัวมันเอง แต่จะเป็นเครื่องมือที่ทรงพลังที่จะช่วยให้โลกยั่งยืนและยกระดับชีวิตประจำวันของผู้คนให้ดียิ่งขึ้น
พบกับซีเมนส์ที่งาน #ThailandSpaceWeek 2024 ในวันที่ 7 – 9 พฤศจิกายน 2567 ที่อิมแพค เมืองทองธานี ภายใต้แนวคิด “Converging Technologies, Connecting People” โดยซีเมนส์ได้นำเทคโนโลยีจากแพลตฟอร์มธุรกิจดิจิทัลแบบเปิด #SiemensXcelerator ร่วมจัดแสดง
ที่งาน #ThailandSpaceWeek 2024 ซึ่งจัดโดยสำนักงานพัฒนาเทคโนโลยีอวกาศและภูมิสารสนเทศ (องค์การมหาชน) หรือ #GISTDA ซีเมนส์จะนำเทคโนโลยีซึ่งครอบคลุมถึงชุดผลิตภัณฑ์ซอฟต์แวร์ที่รองรับการพัฒนากิจการอวกาศทุกด้าน ตั้งแต่การออกแบบเชิงระบบ (System Design), การทดสอบและจำลอง (Simulation & Testing), การบริหารวงจรชีวิตผลิตภัณฑ์ (PLM – Product Lifecycle Management) ไปจนถึงการจัดการกระบวนการผลิต (Manufacturing) ภายใต้แนวคิด Model-Based Systems Engineering (MBSE) และ Digital Threads ที่มีบทบาทสำคัญในการเชื่อมโยงทุกขั้นตอนเข้าด้วยกันตั้งแต่การออกแบบไปจนถึงการผลิตของการพัฒนาระบบดาวเทียมและเทคโนโลยีอวกาศ
From Space Missions to Smart Factories
Personal computers, GPS, mobile phones, digital cameras, the internet: many of the technologies in our lives today are older than we might think. They originate from concepts from the 1960s and 70s – an enormously creative, innovative period.
Another innovation on everyone’s mind is the digital twin which many scientists and engineers today describe as the backbone of a new industrial revolution. A digital twin is a virtual representation of a physical object. This digital counterpart enables real-time monitoring, diagnostics and predictive maintenance, which significantly increases operational efficiency.
Physical models of NASA spacecrafts – the precursors of digital twin
The initial idea of this technology has its origins in NASA – National Aeronautics and Space Administration space missions around 60 years ago. Space missions were expensive and risky, so people preferred to simulate on safe ground what they would have to be prepared for in space.
A simple idea was born, and this is still the key benefit of digital twin today. The term itself was only popularized late, in 2010 to be precise, by NASA´s Michael Grieves and John Vickers. Thereby marking its transition from a tool used in space exploration to an industrial revolution.
The rise of the digital twin and the IoT
If the digital twin is the backbone of the industry of the future, then data is the life blood of the digital twin. The more data, the more precise the digital representation and the more opportunities arise. IoT (Internet of Things) devices, which are being deployed everywhere in our world in exploding numbers, provide precisely this data, which is used intelligently for digital twin.
According to Statista, there are already 15.9 billion IoT devices in use worldwide, and this figure is expected to more than double by 2033. Many of these are already being used in industrial plants and production facilities enabling engineers to simulate every aspect in the virtual environment, from the products themselves to the machines and entire production lines.
Siemens drives the development forward since the early days
Siemens has played a significant role in space exploration through its software and digital solutions which have since found transformative applications in manufacturing.
In the 1970s, Siemens was already focusing on data processing technologies and since then its early technological advancements such as automation and control systems and digitalization laid the foundation for the technologies that power the IoT today. Digital twin technology was originally designed to simulate and monitor complex systems in space. By creating a digital replica of physical assets, engineers could predict how spacecraft components would respond to the extreme conditions of space.
Today, Siemens applies digital twin in manufacturing to optimize production lines, anticipate maintenance needs, and reduce downtime. By enabling virtual testing and refinement of systems, manufacturers can improve efficiency, reduce waste, and achieve high precision without risking costly real-world trial-and-error.
In 2012, Siemens collaborated with NASA on the Mars mission “Curiosity.” The company provided the software solutions that were used to develop, simulate, and test the Mars rover. In 2015, Siemens introduced the concept of digital twin for industrial use at Hannover Fair in Germany and presented the technology for different branches of industry, including the process industries and machine building.
The foundation of Industry 4.0 and the future of smart, sustainable factories
Digital twin is now at the heart of the much talked about Industry 4.0 – the culmination of the digitalization of industrial processes. Digital twin is not only relevant during ongoing operations, but also from the very first minute an idea or business model is created.
Today, a smart factory is first created as a digital twin and only much later in the real world. Precise simulations not only make it possible to avoid roadblocks and foresee dangers, but also to design all processes as efficiently as possible so that the factory of the future is not only productive, but above all highly sustainable.
And yet this is just the beginning: the combination of digital twin and AI will enable computers to independently design optimized products and processes and proactively support decision-makers in industries in their innovations and planning, operations and maintenance.
Combining the real and the digital worlds
The digital twin is a prime example of what it means to connect the real with the digital worlds to create a sustainable impact. By creating digital replicas of physical assets, businesses gain insights that allow them to optimize processes, predict challenges, and innovate responsibly.
For all, it is important to understand that physical reality and the human being at its center will always be the point of reference. Digitalization, like AI, is never a purpose, but no more but also no less than a powerful enabler to transform the everyday for the better.
Experience firsthand Siemens’ pioneering software solutions for aerospace industry at Thailand Space Week 2024 during 7-9 November 2024 at IMPACT Muang Thong Thani.
Organized by the Geo-Informatics and Space Technology Development Agency (GISTDA) under the theme “Converging Technologies, Connecting People”, Siemens will showcase technology from the open digital business platform #SiemensXcelerator, including a comprehensive suite of software products supporting all areas of aerospace development, from System Design, Simulation & Testing, and Product Lifecycle Management (PLM) to Manufacturing Process Management, under the Model-Based Systems Engineering (MBSE) and Digital Threads concepts. These solutions play a vital role in linking every step from design to production in satellite systems and space technology development.